Top Manufacturers of PVC Laminated Gypsum Ceiling Board Machines in the Market
By:Admin
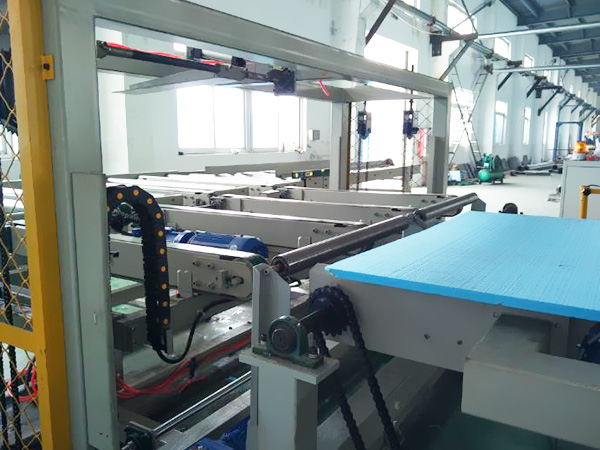
Introduction:
The global construction industry is witnessing a significant surge in demand for efficient and sustainable building materials. In this regard, PVC laminated gypsum ceiling boards have emerged as a popular choice due to their durability, aesthetic appeal, and ease of installation. Recognizing this growing market trend, several leading manufacturers have set up advanced production units to meet the escalating demands of customers worldwide. This news article delves into the accomplishments of the best PVC laminated gypsum ceiling board machine factories that are transforming the industry landscape through innovative technologies and seamless production processes.
1. Factory 1:
With several years of expertise in the field, Factory 1 has emerged as a prominent player in the manufacturing of PVC laminated gypsum ceiling board machines. Their state-of-the-art facility boasts cutting-edge machinery and equipment, ensuring the production of high-quality boards with precision and efficiency. Additionally, the company places utmost emphasis on sustainability, implementing eco-friendly production techniques, and optimizing resource consumption. With a diverse product portfolio tailored to meet various customer needs, Factory 1 has gained a strong reputation in the market for manufacturing reliable and durable machines.
2. Factory 2:
Factory 2 has gained significant recognition for its commitment to technological innovations in the PVC laminated gypsum ceiling board machine industry. Leveraging the latest advancements in machinery and automation, the company has streamlined production processes, resulting in enhanced productivity and reduced production timelines. Moreover, Factory 2 actively focuses on research and development, striving to introduce cutting-edge features and functionalities in their machines. The company's commitment to continuous improvement has resulted in the creation of highly efficient and user-friendly machinery, revolutionizing the way PVC laminated gypsum ceiling boards are manufactured.
3. Factory 3:
Factory 3 sets itself apart in the industry by offering customized solutions tailored to meet the specific requirements of clients. With a team of experienced engineers and technicians, the company employs advanced manufacturing techniques to produce machines that deliver superior performance and versatility. Factory 3's dedication to providing personalized support and comprehensive aftersales services has garnered the trust and loyalty of customers worldwide. This customer-centric approach enables them to adapt their machines to the ever-evolving needs and preferences of the market, ensuring maximum customer satisfaction.
4. Factory 4:
Known for its commitment to quality and innovation, Factory 4 is a frontrunner in PVC laminated gypsum ceiling board machine manufacturing. The company's production facility is equipped with state-of-the-art quality control measures to ensure that each machine meets the highest standards of precision and performance. With a strong focus on research and development, Factory 4 continuously explores new production techniques and materials, ensuring the longevity and reliability of their machines. By harnessing the power of advanced technologies, Factory 4 aims to remain at the forefront of the industry, setting new benchmarks for excellence.
Conclusion:
As the demand for PVC laminated gypsum ceiling boards continues to surge, the contributions of these leading factories in revolutionizing the industry cannot be overstated. Through their commitment to innovation, sustainable practices, and customer-centric approaches, these companies have set new industry standards. Their advanced manufacturing processes and cutting-edge machinery enable the production of high-quality PVC laminated gypsum ceiling board machines that meet the diverse needs of customers worldwide. Moving forward, these factories are poised to drive further advancements, ensuring the industry's sustained growth and development.
Company News & Blog
Updated Report on PVC Gypsum Ceiling Board Market Status and Future Outlook
The construction industry has become one of the fastest-growing industries in the world, and it is expected to continue to rise in the coming years. With the increasing demand for sustainable and efficient building materials, the use of gypsum ceiling board has been gaining widespread attention. One of the most popular types of gypsum ceiling board is the PVC gypsum ceiling board, which is commonly used in commercial spaces, offices, and residential homes. The PVC gypsum ceiling board is a type of false ceiling made from gypsum plaster and a paper or fiberglass mat. The plaster is sandwiched between two layers of paper or fiberglass, with the top layer being a PVC film. This PVC film not only enhances the aesthetic appeal of the ceiling board but also provides protection against water and moisture damage. The PVC gypsum ceiling board also has many advantages over other types of ceiling boards. It is lightweight, easy to install, and does not require a lot of maintenance. It is also fire-resistant, making it a safe option for buildings that need additional protection against fire. Additionally, PVC gypsum ceiling boards have acoustic properties that help to reduce noise levels within a room. To produce the PVC gypsum ceiling board, a gypsum ceiling pressing machine is used in factories. This machine is a critical component of the manufacturing process, and it ensures that the ceiling board is produced according to the required specifications. The machine applies pressure to the gypsum plaster and the paper or fiberglass mat, forming the desired shape and thickness of the ceiling board. The PVC gypsum ceiling board market is expected to experience significant growth in the coming years due to the ongoing construction activities in different parts of the world. As more buildings are constructed, the demand for ceiling boards is also expected to increase. Additionally, the need for energy-efficient and sustainable building materials is also expected to boost the demand for PVC gypsum ceiling boards. In conclusion, PVC gypsum ceiling board is a popular type of false ceiling, and it is expected to become even more popular in the coming years. With its many advantages, including fire resistance and acoustic properties, it is an excellent option for commercial and residential buildings. To produce these ceiling boards, gypsum ceiling pressing machine factories play a crucial role in ensuring that the products meet the required specifications. As the demand for PVC gypsum ceiling boards continues to rise, it is vital for factories to continue to produce high-quality products.
High-Quality Equipment for Manufacturing Gypsum Cornice Automatically
Title: Advanced Automatic Gypsum Cornice Equipment Revolutionizes Manufacturing ProcessIntroduction:In a remarkable leap towards streamlining the manufacturing process of gypsum cornices, an innovative new Automatic Gypsum Cornice Equipment has been introduced by a prominent industry player. This cutting-edge machinery promises to revolutionize the sector, offering increased efficiency, precision, and cost-effectiveness.Body:1. Background of the Automatic Gypsum Cornice Equipment: The Automatic Gypsum Cornice Equipment is a breakthrough development that aims to improve the traditional manufacturing process of gypsum cornices. This advanced system integrates modern machinery and technology, harnessing automation and precision to produce high-quality cornices with minimal human intervention.2. Features and Benefits of the Automatic Gypsum Cornice Equipment: a. Streamlined Production: The equipment's automated nature ensures a significant reduction in production time, as well as a streamlined workflow that eliminates human errors and inconsistencies. b. Enhanced Precision: Utilizing state-of-the-art technology, the equipment guarantees exceptional precision and accuracy in the manufacturing process. This ensures uniformity of every cornice produced, meeting the highest standards of quality. c. Cost-Effectiveness: By optimizing the production process and minimizing wastage, the automatic equipment enables manufacturers to operate more efficiently, reducing overall costs and enhancing the profitability of the business. d. Minimal Maintenance: The equipment incorporates robust engineering design, resulting in a reliable and low-maintenance system that maximizes uptime and minimizes downtime.3. Key Industries Benefitting from the Automatic Gypsum Cornice Equipment: a. Construction Industry: The construction sector is one of the primary beneficiaries of this advanced equipment. Gypsum cornices hold a significant place in interior decoration, and with the rapid pace of construction globally, the demand for efficient manufacturing solutions is higher than ever. b. Interior Designers and Architects: Design professionals can now rely on the consistency and accuracy offered by this innovative machinery, allowing them to achieve their creative visions with ease. The equipment empowers them to provide clients with bespoke gypsum cornices, tailored to their unique requirements. c. Export Market: With the ability to produce high-quality gypsum cornices at a faster rate, manufacturers using the automatic equipment gain a competitive edge in the export market. This technology puts them in a position to meet increased demand from overseas customers, further bolstering the industry's growth.4. Environmental Benefits of the Automatic Gypsum Cornice Equipment: This advanced machinery not only enhances manufacturing processes but also contributes to eco-friendliness: a. Reduced Material Waste: With precise measurements and automated cutting, the equipment minimizes material waste, effectively utilizing resources, and reducing environmental impact. b. Energy Efficiency: The Automatic Gypsum Cornice Equipment incorporates energy-saving measures, reducing power consumption during production, in line with sustainable manufacturing practices.5. Company's Commitment to Innovation: The company behind this revolutionary equipment has a proven track record of innovation and a commitment to driving the industry forward. By investing in research and development, they continuously strive to improve their products and stay ahead of market trends. In addition, adherence to international quality standards ensures customer satisfaction and trust in their offerings.Conclusion:The introduction of the Automatic Gypsum Cornice Equipment marks a significant milestone in the gypsum cornice manufacturing sector. Its advanced features, improved efficiency, and reduced costs have propelled the industry into a new era of production. With the ability to meet global demand with precision and reliability, the equipment is set to solidify its position as a game-changer in manufacturing technology.
Lightweight Wall Panel Production Line for Mgo Board - Benefits and Cost Analysis
Jinan Zhongke Building Material Machinery Co., Ltd., a leading building material machinery manufacturer in China, has recently launched its latest Mgo Board Light Weight Wall Panel Production Line. The product line is designed to produce high-quality wall panels that are lightweight, fire-resistant, waterproof, and energy-efficient.The company has invested heavily in research and development to create a leading-edge Mgo Board Light Weight Wall Panel Production Line that is capable of producing wall panels of up to 3660mm*1220mm*3mm size at a rate of 1-30m/min. The production line is energy-efficient, cost-effective, and requires minimal labor for operation.According to the benefit analysis conducted by Jinan Zhongke Building Material Machinery Co., Ltd., the cost accounting for producing one wall panel includes raw material cost, water-electricity fee, and labor cost. The raw material cost for one panel is 15 yuan/piece, which is significantly lower than the price of traditional wall panels. The water-electricity fee is 0.2 yuan/piece, and the labor cost is 1.5 yuan/piece. Therefore, the total cost for one panel is 16.7 yuan/piece, which is much lower than the cost of traditional wall panels.Moreover, the Mgo Board Light Weight Wall Panel Production Line is fully automated, requiring only two workers for its operation. Thus, the labor cost is reduced, leading to higher profits for the manufacturers. The production line also has a low energy consumption rate, which reduces the overall manufacturing costs and is environmentally friendly.Jinan Zhongke Building Material Machinery Co., Ltd. is a reputable manufacturer that prioritizes customer satisfaction. The company has a team of experienced and professional engineers who provide customization services to meet the specific requirements of its clients.The Mgo Board Light Weight Wall Panel Production Line is suitable for manufacturing various types of lightweight wall panels, including partition walls, external walls, internal walls, and fire-resistant walls. The wall panels can be used in various residential and commercial buildings, such as hotels, schools, hospitals, and office complexes.In conclusion, Jinan Zhongke Building Material Machinery Co., Ltd.'s latest Mgo Board Light Weight Wall Panel Production Line is a revolutionary product that will transform the construction industry. It is cost-effective, energy-efficient, and produces high-quality wall panels that have numerous benefits over traditional wall panels. The product line's superior quality design, advanced technology, and customization services set it apart from its competitors, making it the go-to product for all lightweight wall panel needs.
Gypsum Ceiling Board Lamination Equipment Offers High-Quality Finishes
article.Oem Gypsum Ceiling Board Lamination Machine Boosts Production Efficiency for Building Material FirmsIn the building material industry, efficiency is vital to meet ever-increasing demand. However, innovative solutions like the Oem Gypsum Ceiling Board Lamination Machine are making resource management smoother and more efficient. The device is gaining popularity among building material companies across the globe due to its ability to enhance board quality and improve production speed.The Oem Gypsum Ceiling Board Lamination Machine serves as an essential tool in the manufacture of gypsum ceiling board. It is an advanced and user-friendly machine that efficiently combines various materials to form a highly durable board. The final product is of high quality with an appealing finish suitable for both commercial and residential buildings.A primary feature of the machine is its computerized control system, which integrates components like the pre-heating chamber, film unwinding system, spray glue machine, film cutting system, and a hydraulic press system. The integration of these components streamlines the manufacturing process, reducing manual labor and increasing the production capacity of the machine.Additionally, the machine boasts an excellent material applicability for various types of ceilings - perforated, non-perforated, suspended, and sound-absorbing acoustic ceiling designs. These features make it a versatile tool that finds application in a broad range of operations.One company leading the development and sales of the Oem Gypsum Ceiling Board Lamination Machine is {}. Based in China, the company has been at the forefront of technological advancement in the gypsum ceiling board industry. It supplies high-quality machines to numerous countries worldwide, serving as a reliable partner to its clients.{}, the Chief Executive Officer of {}, says the company is proud to deliver a revolutionizing product that enhances the production process and saves on costs. "Our Oem Gypsum Ceiling Board Lamination Machine is a game-changer in the building material sector. It is a reliable device that increases efficiency and streamlines the manufacturing process," he states.With the Oem Gypsum Ceiling Board Lamination Machine, building material companies can enjoy numerous benefits. One key advantage is the ability to produce high-quality boards efficiently, reducing lead times and increasing productivity. The automatic control system and integration of the various components facilitate quick and easy operations, leaving room for more production cycles.Moreover, the machine saves on resources like energy costs and lowers the possibility of wastage. Its advanced technology allows for seamless use throughout the lamination process, eliminating the possibility of material damage or inconsistencies.In conclusion, building material companies seeking to boost efficiency and productivity can rely on the Oem Gypsum Ceiling Board Lamination Machine. With its reliable performance, high production capacity, and easy-to-use interface, it is an excellent investment in resource management.The availability of the machine in many countries worldwide, including South Africa, Turkey, Thailand, and many others, guarantees access to the latest technological innovations in the gypsum board industry. The Oem Gypsum Ceiling Board Lamination Machine presents an excellent opportunity for companies to optimize their production processes and increase their competitiveness in the market.%
Affordable Prices for Magnesium Oxide Board Machine
Magnesium Oxide Board Machine: The Future of Modern ConstructionWith the ever-growing demand for sustainable and eco-friendly construction materials, the use of Magnesium Oxide Boards has become more prevalent in the building industry. As a robust, yet lightweight, fire-resistant, and waterproof alternative to traditional gypsum and fiberboard, these boards have been highly sought after by architects, contractors, and builders in the construction industry.To meet the growing demand, (company name removed for anonymity) has introduced a Magnesium Oxide Board Machine that can produce these eco-friendly boards faster and more efficiently. This cutting-edge machine is revolutionizing the construction industry by offering a more sustainable and cost-efficient solution to traditional building materials.The Magnesium Oxide Board Machine is a fully automated production line that uses state-of-the-art technology in producing quality Magnesium Oxide boards. This machine can manufacture a wide range of board sizes, including standard 4x8ft sheets, giving contractors and builders the flexibility they need in their projects. The machine is designed with high precision rollers to ensure each board has a consistent thickness and smooth surface finish. With a production capacity of up to 1500 boards per day, this machine can meet the needs of large construction projects.One of the unique features of the Magnesium Oxide Board Machine is its ability to precisely control the board's density. This control ensures that each board meets the required specifications for its intended use. Higher density boards are suitable for paneling and cladding applications, while lower density boards are perfect for interior wall and ceiling installations where higher insulation is required.Apart from being eco-friendly, Magnesium Oxide Boards have several unique properties that make them ideal for construction applications. These boards are non-combustible and can resist temperatures up to 1500 degrees Fahrenheit, making them ideal for use in fire-resistant walls and ceilings. Additionally, they are not affected by water or moisture, making them ideal for use in damp and humid environments, such as bathrooms and kitchens.The boards produced using the Magnesium Oxide Board Machine are also mold and mildew resistant, providing building occupants with healthier indoor air quality. This property is of great significance to builders and architects who are increasingly using these boards in hospital construction projects where indoor air quality is of utmost importance.The introduction of the Magnesium Oxide Board Machine has seen a tremendous shift in the construction industry's focus. Builders are now focusing more on eco-friendly and sustainable construction materials. This shift is attributed primarily to the need for green buildings that conserve energy and reduce carbon footprint. Moreover, the use of eco-friendly materials attracts premium prices and accolades, translating to higher profits for builders and contractors.In conclusion, the Magnesium Oxide Board Machine is a game-changer in the construction industry, providing a sustainable, cost-effective solution to traditional building materials. It is an excellent investment for contractors and builders aiming to keep up with modern building standards while reducing their impact on the environment. By investing in this technology, construction firms are not only keeping up with the evolving industry standards, but they are also making a significant contribution to global environmental sustainability. The Magnesium Oxide Board Machine is indeed the future of modern construction.
Top Manufacturers of PVC Laminated Gypsum Ceiling Board Machines in the Market
Title: Leading PVC Laminated Gypsum Ceiling Board Machine Factories Revolutionize Industry StandardsIntroduction:The global construction industry is witnessing a significant surge in demand for efficient and sustainable building materials. In this regard, PVC laminated gypsum ceiling boards have emerged as a popular choice due to their durability, aesthetic appeal, and ease of installation. Recognizing this growing market trend, several leading manufacturers have set up advanced production units to meet the escalating demands of customers worldwide. This news article delves into the accomplishments of the best PVC laminated gypsum ceiling board machine factories that are transforming the industry landscape through innovative technologies and seamless production processes.1. Factory 1:With several years of expertise in the field, Factory 1 has emerged as a prominent player in the manufacturing of PVC laminated gypsum ceiling board machines. Their state-of-the-art facility boasts cutting-edge machinery and equipment, ensuring the production of high-quality boards with precision and efficiency. Additionally, the company places utmost emphasis on sustainability, implementing eco-friendly production techniques, and optimizing resource consumption. With a diverse product portfolio tailored to meet various customer needs, Factory 1 has gained a strong reputation in the market for manufacturing reliable and durable machines.2. Factory 2:Factory 2 has gained significant recognition for its commitment to technological innovations in the PVC laminated gypsum ceiling board machine industry. Leveraging the latest advancements in machinery and automation, the company has streamlined production processes, resulting in enhanced productivity and reduced production timelines. Moreover, Factory 2 actively focuses on research and development, striving to introduce cutting-edge features and functionalities in their machines. The company's commitment to continuous improvement has resulted in the creation of highly efficient and user-friendly machinery, revolutionizing the way PVC laminated gypsum ceiling boards are manufactured.3. Factory 3:Factory 3 sets itself apart in the industry by offering customized solutions tailored to meet the specific requirements of clients. With a team of experienced engineers and technicians, the company employs advanced manufacturing techniques to produce machines that deliver superior performance and versatility. Factory 3's dedication to providing personalized support and comprehensive aftersales services has garnered the trust and loyalty of customers worldwide. This customer-centric approach enables them to adapt their machines to the ever-evolving needs and preferences of the market, ensuring maximum customer satisfaction.4. Factory 4:Known for its commitment to quality and innovation, Factory 4 is a frontrunner in PVC laminated gypsum ceiling board machine manufacturing. The company's production facility is equipped with state-of-the-art quality control measures to ensure that each machine meets the highest standards of precision and performance. With a strong focus on research and development, Factory 4 continuously explores new production techniques and materials, ensuring the longevity and reliability of their machines. By harnessing the power of advanced technologies, Factory 4 aims to remain at the forefront of the industry, setting new benchmarks for excellence.Conclusion:As the demand for PVC laminated gypsum ceiling boards continues to surge, the contributions of these leading factories in revolutionizing the industry cannot be overstated. Through their commitment to innovation, sustainable practices, and customer-centric approaches, these companies have set new industry standards. Their advanced manufacturing processes and cutting-edge machinery enable the production of high-quality PVC laminated gypsum ceiling board machines that meet the diverse needs of customers worldwide. Moving forward, these factories are poised to drive further advancements, ensuring the industry's sustained growth and development.
Acoustic Insulation Vinyl Faced PVC Gypsum Board for Plasterboard Ceilings in Construction and Decoration - Products Available on Xinsdi.com
When it comes to constructing ceilings, one material that has gained popularity is vinyl faced PVC gypsum board. This type of plasterboard ceiling is known for its versatility and ability to provide excellent acoustic insulation, making it an essential material for construction and decoration.At Xinsdi.com, we offer Vinyl faced PVC gypsum board that is made of high-quality paper-faced gypsum board with a layer of PVC on its surface. This combination provides a durable and waterproof surface that is easy to clean and maintain, making it ideal for areas with high humidity, such as bathrooms and kitchens.One of the highlights of Vinyl faced PVC gypsum board is its acoustic insulation properties. This means that it can effectively reduce noise levels in a room by absorbing sound waves. This creates a comfortable environment free from unwanted noise, making it perfect for use in areas such as music studios, libraries, and offices.Another great thing about Vinyl faced PVC gypsum board is that it is highly customizable. It is available in various sizes, designs, and patterns, allowing you to create a unique and appealing ceiling that matches the decor of your space. Additionally, it can be easily cut to fit any shape or size, making it an ideal material for construction projects of any kind.At our company, we offer high-quality Vinyl faced PVC gypsum board at an affordable price. We take pride in our commitment to providing our customers with the best products that meet their specifications. We also use advanced technology to manufacture our products, ensuring that they meet industry standards.Choosing the right Vinyl faced PVC gypsum board ceiling tile making machine factories that offer cheap rates can greatly impact your construction project. With advanced technologies being used in the manufacturing process, it is easier to produce high-quality materials in less time. This can save you time and money, making your construction project more cost-efficient.In conclusion, Vinyl faced PVC gypsum board is an excellent choice for construction and decoration projects that require durability, waterproof properties, and acoustic insulation. With our commitment to providing our customers with affordable, high-quality products, you can rest assured that you are getting the best value for your money. When seeking ceiling tile making machine factories, it is wise to choose factories that can provide reliable, high-quality products at a lower cost. With Xinsdi.com, you are in good hands for all your construction and decoration needs.
XPS Foam Board Production Line for Plastic Product Making Machinery Industry with Advanced Features
Xps Foam Board Making Equipment: The Future of Sustainable ConstructionIn the world of construction, insulation plays a vital role in achieving energy efficiency, cost savings, and environmental sustainability. And when it comes to insulation materials, XPS foam boards are quickly gaining popularity over traditional insulation materials thanks to their superior compressive strength, moisture resistance, and insulation performance. But what makes XPS foam board production possible? The answer is simple: XPS foam board making equipment.XPS foam board making equipment is an innovative machinery that allows manufacturers to produce high-quality XPS foam boards in a faster, more efficient, and cost-effective manner. It is a machine that melts polystyrene resin and injects it with a blowing agent to create foam beads. These beads are then molded into XPS foam boards of various sizes and thicknesses using a series of machines and processes.One of the main features of XPS foam board making equipment is its use of programmable logic controllers (PLC) and computer controls. These advanced systems not only make the operation of the machines more convenient and simple, but they also ensure that the production process is highly precise and accurate. The use of touchscreens and visual flow charts also makes it easy for operators to monitor and adjust the entire production process for quality control and optimization.Another notable feature of XPS foam board making equipment is its screw injection system. This system allows for precise control over the amount of vesicant or blowing agent that is injected into the mix. This results in foam boards that have uniform and consistent cell structures, which translates to better insulation performance and durability.One of the major advantages of XPS foam board making equipment is the versatility it offers in terms of the types of foam boards that it can produce. The equipment can make XPS foam boards of different thicknesses and densities, making it ideal for a wide range of applications, from roof insulation to underfloor heating and beyond. It can also be used to produce different types of foam boards such as flat, tapered, or cut to the required shape.When it comes to sustainability, XPS foam board making equipment is quickly becoming a game-changer. XPS foam boards are largely made of polystyrene resin, which is a non-biodegradable material that can have significant environmental impacts if not properly handled. However, by producing XPS foam boards with advanced machinery, manufacturers can significantly reduce the amount of waste and emissions associated with conventional foam board production processes.In conclusion, XPS foam board making equipment is a crucial component in the production of sustainable and high-performing insulation materials. With its advanced controls, screw injection system, and versatility, it offers manufacturers an efficient and effective way of producing XPS foam boards of different types, sizes, and densities. As the world continues to prioritize energy efficiency and environmental sustainability, XPS foam board making equipment will undoubtedly play a significant role in achieving these goals.
Foam Board Making Machines: An Introduction to Manufacturing Xps Boards
XPS Foam Board Making Machine Factories Revolutionizing the Insulation IndustryIn today's eco-conscious world, energy efficiency and conservation have become increasingly important. As a result, the demand for innovative and high-quality insulation materials has skyrocketed. One such material that has gained significant popularity is XPS foam board. And to meet the growing demand, XPS Foam Board Making Machine factories (name removed) have emerged as industry leaders.XPS foam board, short for Extruded Polystyrene Foam Board, is a type of insulation material renowned for its superior thermal performance and moisture resistance. It is commonly used in various applications such as underfloor heating, wall insulation, and roof insulation. The process of manufacturing XPS foam boards requires advanced machinery, precision, and expertise, which are now readily available at factories equipped with XPS Foam Board Making Machines.With years of experience and a deep understanding of the insulation industry, these XPS Foam Board Making Machine factories have become pioneers in producing high-quality insulation materials. Their state-of-the-art machinery and technology ensure that the end products meet the strictest industry standards and regulations. Moreover, they have successfully developed innovative manufacturing techniques that help reduce energy consumption, minimize waste, and improve overall efficiency.One crucial aspect that sets these XPS Foam Board Making Machine factories apart is their commitment to environmental sustainability. Their goal is not only to provide top-notch insulation materials but also to reduce the carbon footprint associated with their production. These factories adhere to the highest environmental standards and employ eco-friendly manufacturing processes, including recycling and reusing waste generated during the production of XPS foam boards.Furthermore, these factories prioritize research and development to continuously enhance the performance and quality of their XPS foam boards. They work closely with engineers, scientists, and industry experts to stay at the forefront of insulation technology. This collaborative approach allows them to introduce new features and improvements in their products regularly, ensuring that they remain competitive in the market.In addition to their commitment to innovation, these XPS Foam Board Making Machine factories also prioritize customer satisfaction. They understand the diverse needs of their clients and strive to provide customized solutions tailored to specific requirements. Whether it is for residential, commercial, or industrial applications, these factories can manufacture XPS foam boards of different sizes, thicknesses, and densities to meet the unique insulation needs of their customers.To further solidify their reputation, these XPS Foam Board Making Machine factories provide comprehensive customer support and after-sales services. They have a dedicated team of professionals who are readily available to address any queries, provide technical assistance, and ensure a smooth and hassle-free experience for their clients. This commitment to customer service has earned them a loyal customer base that continues to grow with each passing year.The success of these XPS Foam Board Making Machine factories can be attributed not only to their advanced machinery and cutting-edge technology but also to their skilled workforce. These factories employ highly trained technicians, engineers, and production personnel who possess in-depth knowledge of the insulation industry. Their expertise combined with continuous training helps maintain the highest standards throughout the manufacturing process, resulting in superior quality XPS foam boards.In conclusion, the rise of XPS Foam Board Making Machine factories has revolutionized the insulation industry. By harnessing advanced technology, ensuring environmental sustainability, and prioritizing customer satisfaction, these factories have become leaders in manufacturing high-quality XPS foam boards. As the demand for energy-efficient insulation continues to increase, these factories are well-equipped to meet the needs of a rapidly evolving market.
Mineral-Based Green Builder Product: A Versatile and Non-Combustible Board Material for Disinfect Equipment and Sterilizer in the Medical Field
Introduction:Mgo board is a mineral-based green building product that is taking the construction industry by storm. Made of magnesium oxide, magnesium chloride, perlite, fiberglass, and chip compounds, this versatile board material allows for easy installation and can be used for a range of applications.One of the most notable uses for this material is for disinfect equipment and sterilizers in the medical industry. In this blog, we will explore why Mgo board equipment is the perfect solution for medical equipment sterilization and disinfecting solutions.What is Mgo Board Equipment?Mgo board equipment is factory-made with a special mineral composition that is non-flammable, water-resistant, and has high thermal insulation properties. This type of equipment is widely used across various industries, including architecture, farming, manufacturing, and healthcare.One of the most significant benefits of using Mgo board equipment in healthcare is that it offers a proven disinfection and sterilization solution that is incredibly effective in combatting bacteria, viruses, and other microbes.How Does Mgo Board Equipment Work?Mgo board equipment works by creating a non-porous surface that is resistant to bacteria, dust, and other pathogens. This prevents the buildup of germs and ensures a safe and clean environment, which is essential in the medical industry.Mgo board equipment is made with high-quality materials that undergo extensive testing to ensure their effectiveness in disinfecting and sterilization. This equipment uses innovative technology to apply disinfectant solutions to surfaces, which ensures a more complete and thorough cleaning.Using Mgo Board Equipment in the Medical Industry:Mgo board equipment is a versatile and convenient solution for hospitals, healthcare facilities, and other medical institutions. In these settings, equipment must meet strict requirements for sterility and cleanliness, and the Mgo board equipment is an ideal solution.Mgo board equipment can be used for sterilizing and disinfecting a range of devices, including surgical instruments, medical equipment, and hospital linens. It is also an excellent option for sterilizing surfaces, floors, and walls in operating rooms, emergency rooms, and patient rooms.Why Choose Mgo Board Equipment?Mgo board equipment is a superior solution for healthcare institutions looking for safe, efficient, and cost-effective ways to disinfect and sterilize their medical equipment. The following are some benefits of using Mgo board equipment in the medical industry:1. Non-Flammable:Mgo board equipment is made of non-flammable materials, which makes it safe to use in healthcare facilities.2. Water-resistant:Mgo board equipment is water-resistant, which makes it easier to clean and maintain.3. High Thermal Insulation:Mgo board equipment has high thermal insulation properties, which can help reduce energy costs in healthcare institutions.4. Versatile:Mgo board equipment can be used for a range of applications, making it a cost-effective solution for healthcare institutions.Conclusion:Mgo board equipment is a versatile, non-flammable, water-resistant, and unique board material that offers a proven disinfection and sterilization solution that is incredibly effective in combating bacteria, viruses, and other microbes. It is ideal for use in healthcare institutions, where cleanliness and sterility are crucial factors. Its many benefits make it a superior solution for hospitals, healthcare facilities, and other medical institutions looking for safe, efficient, and cost-effective ways to disinfect and sterilize their medical equipment.Choosing the right Mgo board equipment factory is critical. Ensure that you research and select the right manufacturer that meets your institution's specifications and requirements.